We Measure, We Test, We Assure
At every stage of production, we ensure quality through precise measurements, calibrated equipment, and standardized testing. Our goal is consistency in every product, and confidence in every delivery.
Our extrusion lines, state-of-the-art automatic powder coating systems, manufacturing and assembly facilities add value and quality to aluminum profiles. All our production processes are certified in accordance with international standards. We care for your products, respect the environment, and provide a healthy and safe workplace for our team members.
Thanks to our quality management system and integrated software infrastructure, every process is under control and open to continuous improvement. From raw material to finished product, the entire process is traceable via our digital system, ensuring customer satisfaction.
We control all our processes and products with in-house laboratories and advanced testing equipment.
Some of the key quality control devices we use to meet inspection and certification requirements are as follows:
We provide measurement reports for each order using the NEXUS high-precision photometric profile scanner.
Universal hardness tester
Surface roughness measurement device
Chemical analysis spectrophotometer
Tensile testing machine with pressure testing capability, providing certification reports for each production batch
Additionally, our powder coating lines are tested and verified in a fully equipped chemical laboratory according to QUALICOAT standards.
IMPACT TEST
In the powder coating facility, the impact test is conducted to assess the flexibility and durability of the coating. Any cracks or similar issues detected during the test indicate a potential problem with coating quality.
The coated test panel is placed on the red-marked section of the device, aligned to the impact location. Then, the lock holding the weight at the top is released by turning it to the right, allowing the weight to drop onto the panel. After impact, the weight is lifted and locked back into place. The test panel is examined to determine whether the result is acceptable or not for production.
BENDING TEST
The bending test is used to evaluate the flexibility of the coated surface.
The test panel is placed in the gap at the center of the device. First, the lower long arm is turned to secure the panel in place from below, then the upper long arm is used to lock it from the top. The locked panel is bent backward using the upper arm. After bending, the arms are turned in the opposite direction to release the panel. The results of the bending test are analyzed to provide feedback on the suitability for production.
CUPPING TEST
This test is used to evaluate the coating’s resistance to cracking and delamination from the metal surface.
The painted test panel is placed into the device by rotating the red handles to open the holder, then secured by turning in the opposite direction. The electronic panel is activated using the ON/OFF button, and the black handle on the right is rotated slowly until the panel reads 5 mm. Then it is turned back in the opposite direction until it reaches 0 mm. The panel is released and removed from the device, and the electronic unit is powered off. The tested panel is examined and the results are used to decide whether the part is suitable for production.
CROSS-CUT TEST
The cross-cut test is a mechanical method used to assess how well the coating adheres to the surface.
Based on the coating thickness in microns, a suitable blade (1 mm, 2 mm, or 3 mm) is used to cut a grid pattern (horizontal and vertical lines) on the surface. The test panel is then examined and the result is used to determine if the coating adhesion is sufficient for production.
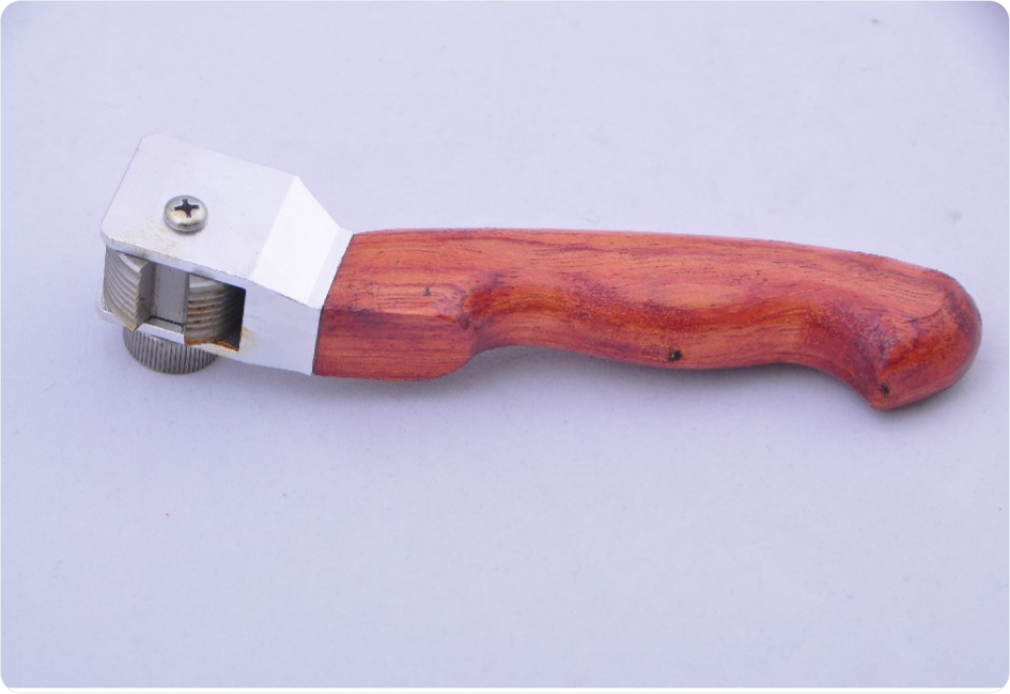
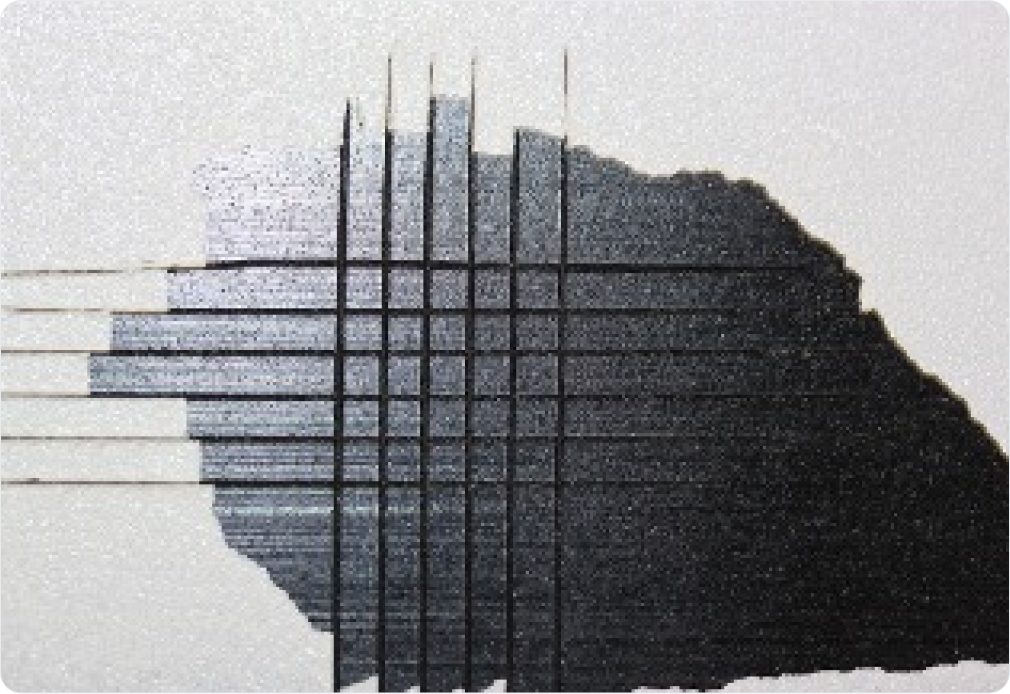
