Perfect Finish, Protected Surface
Surface quality, aesthetics, and durability in one powerful coating solution.

POWDER COATING
Our advanced Wagner electrostatic powder coating technology protects aluminum profiles while giving them a visually appealing finish. With rapid color change capabilities, the system enhances flexibility and reduces both energy and powder consumption—minimizing environmental impact.
The electrostatic spraying method we employ ensures an even and durable coating. This increases resistance to UV radiation, scratches, and abrasions. Thanks to our wide color palette, we can meet diverse aesthetic demands in architectural, automotive, and industrial applications. By combining quality, speed, and eco-conscious production, we deliver a win-win solution for our clients and the planet.
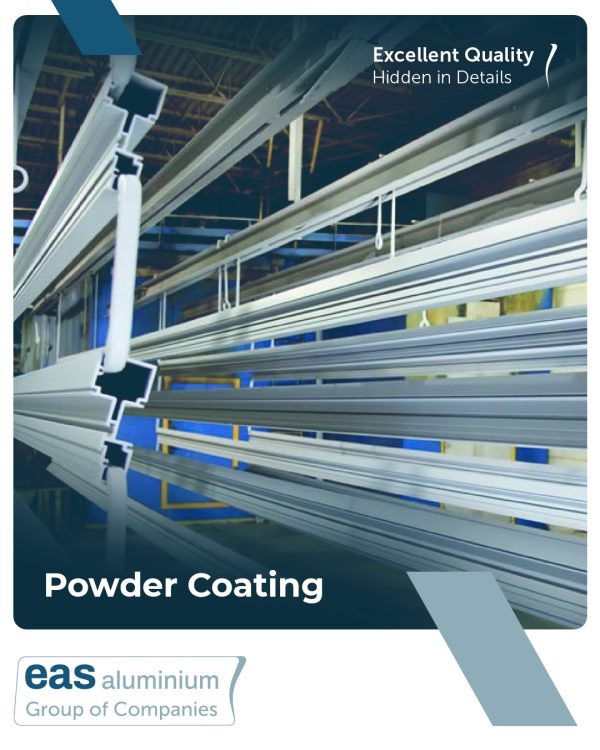
